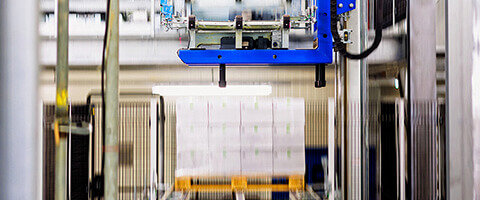
Components
Over the years, we have evolved from a component supplier to a full-service provider. What has remained the same? The guaranteed quality of our products. What's new? Our experience allows us to go higher, faster, longer and heavier. We implement individual wishes and requirements for our customers, regardless of the industry. Being part of the Doppelmayr Group gives us complete flexibility. While almost all moving components are manufactured in the Doppelmayr halls, we can concentrate fully on planning, programming, assembly and commissioning.
Operation and Equipment
We keep our finger on the pulse and are constantly developing our products. All our components are equipped with proven, modular control technology. Robust and dirt-resistant designs, easy expansion options and long product life cycles ensure smooth operation. Thanks to our LIOS Cockpit, our customers always have an overview of all components. To make operation even easier, our systems can now be controlled not only via a stationary HMI, but also conveniently via a mobile tablet in the field.
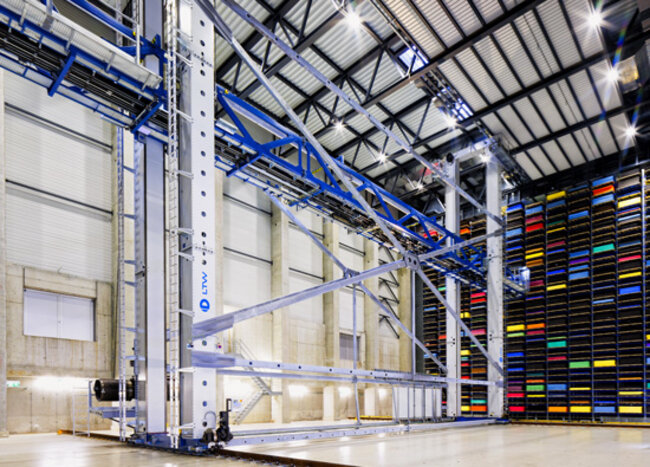
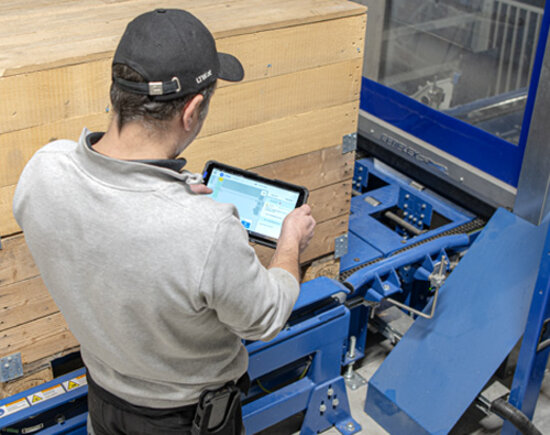
Manual operation is unavoidable in the event of a plant shutdown. Conventional HMIs are often cumbersome and complicated to use. That's why we have taken manual machine control to a new level with the LTW LIOS Mobile Operator. Now it is possible to conveniently control the entire system with a tablet. How is this possible? Thanks to the flexible connection at each control station, the manual operation area opens up in the LIOS Cockpit and you're ready to go. Safety first: Since work can only be performed at the respective operator station, the sophisticated safety concept always knows where the operator is physically located. In addition to mobile operation, the LIOS Cockpit provides a complete overview of the system at all times.

One of our most outstanding quality features? Manufacturing to ropeway standards and being part of the Doppelmayr Group! While almost all moving components are manufactured in the halls of the world market leader in ropeways, we can concentrate fully on the design of the system layout – and there are no limits to our creativity. Whether it's a stacker crane for 31 m long goods, for 18,000 kg containers or for boats – everything is possible for us, from standard pallet warehouses to heavy-duty giants. Not surprisingly, our components can be used in any industry: From the food industry and deep-freeze solutions to the automotive sector and the highly sensitive pharmaceutical industry. We can respond optimally to individual customer requirements.
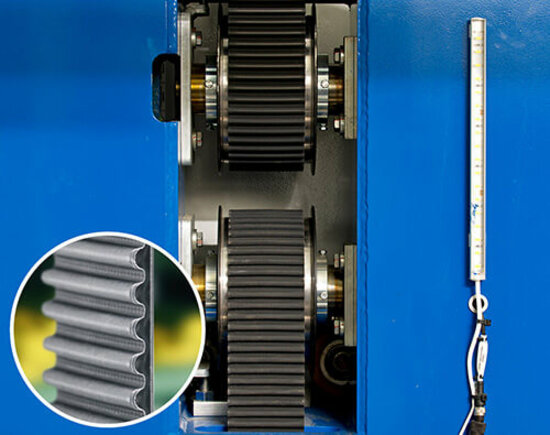
The advantages of our patented belt technology are easy to explain: long service life, short positioning time and maximum performance. Thanks to our dedicated development work, belts are replacing ropes as the lifting medium in more and more applications – and this puts us at the forefront of the market. Although belt technology has been used for years in small parts warehouses, we are already using belts in projects with goods weighing 18,000 kg. And the best thing about it? Our belt can still be used optimally at temperatures between –30°C and +60°C.