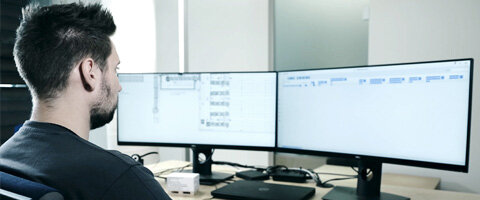
HOTLINE
Customer Care Center
With us, you not only get a first-class intralogistics system, but also a reliable partner for the entire service life of your system. Let our comprehensive services convince you!
Our Customer Care Center ensures that you always receive optimum support – whether it's a classic on-site service call, telephone support, a maintenance call or the procurement of spare parts. We are there for you. Our service team will also support you with the modernization of your system or with training courses perfectly tailored to your needs. Because we are certain: knowledge is the only thing that increases when it is shared.
Customer Care Center Organization Structure
LTW care
the digital service platform
Even better service – with LTWcare, we can ensure customized service throughout the entire life cycle of your system. The maximum performance capacity and availability of the entire system play a central role here, and provide a sound basis for targeted and efficient support. LTWcare includes a wide range of service products from a TÜV-certified remote connection with the highest security standards and an innovative ticket system with state-of-the-art communication options, through proactive maintenance requirements.
Discover LTWcare