Frastanz, Austria
11er Nahrungsmittel
11er Nahrungsmittel GmbH specializes in the production and marketing of frozen potato products. Each year, 80,000 tons of raw potatoes are transformed into quality products such as French fries, potato croquettes, sliced fried potatoes, and filled potato pockets at the Frastanz site in the Austria-Germany-Switzerland border triangle. With 220 employees at its headquarters and exports of 70%, 11er is represented throughout Europe. The quality of production and logistics is certified to many standards: ISO (since 1994), BRC (since 2000), IFS (since 2003), and Ökoprofit (for the third time since 2008).
PROJECT OVERVIEW
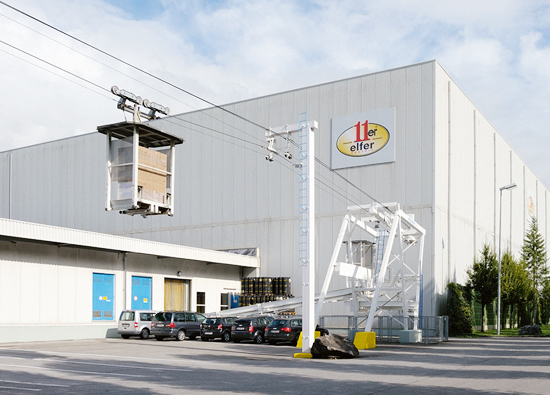
In 1991, the company sets up its third frozen food store, and simultaneously, its first fully automated high-bay warehouse. A specialist equipment supplier for potato processing companies gets the chance to be a full-service provider. Various subcontractors contribute the individual components: three aisle-changing stacker cranes, the conveyor system, an overhead conveyor between production and storage, and the software. Despite these good-quality components, 11er is subsequently faced with interface problems, frequent disruptions, system crashes, and a lack of clarity with regard to supplier responsibility.
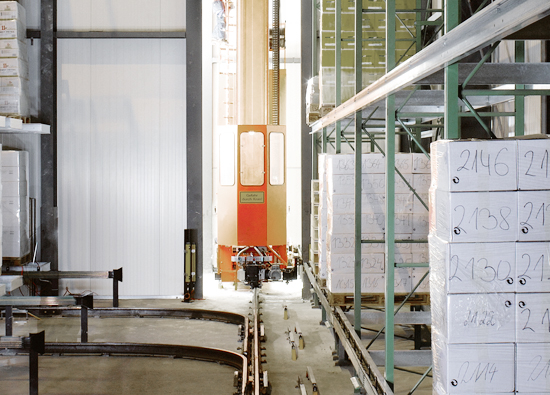
The logistics team at 11er approaches LTW customer service to ask them to take over maintenance for the entire third-party installation. But during the first, joint, on-site visit, a radical modernization project starts to take shape. After more than a decade of operation, the technical systems are outdated, and spare parts are becoming increasingly difficult to find. The stacker cranes, rail system, conveyor system, and control system are to be brought up to the state-of-the-art. The warehouse control system also has to be replaced by new software with an open, lean interface to the 11er ERP system.
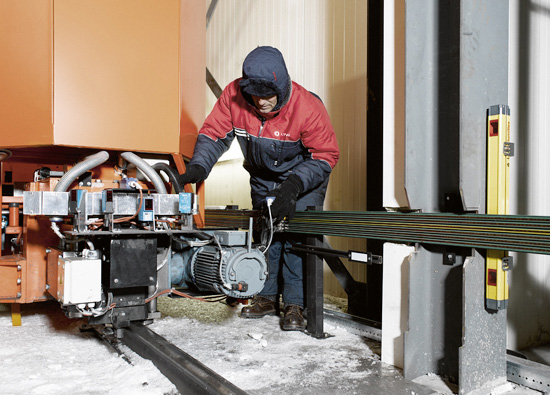
The original suppliers also submit a tender. Although the retrofit package LTW offers is slightly more expensive, the improved performance more than makes up for the extra cost. A detailed on-site analysis does the rest. It takes less than three weeks to complete the installation work. The plant is at a standstill, apart from the air conditioners. Temperatures of -28°C are highly demanding of the team and the tools, especially for work requiring fine motor skills. The scheduled reserve day is not needed in the end; the interface between the LTW warehouse control system and the 11er ERP system works straightaway.