Bludesch, Austria
Hämmerle Kaffee GmbH
Hämmerle Kaffee is a successful, family-run coffee producer based in Bludesch, Austria, and counts among the top brands in the international vending machine goods sector. Since 1972 Hämmerle has been producing and selling a wide variety of high-quality products for vending machines, such as coffee, hot chocolate, cappuccino, topping powders, and tea. Originally 'only' produced to fill vending machines, the company soon developed a business area dedicated to these products. Today, they supply the vending machine sector, retailers, and large consumers around the world with their Ragazza range or custom private label products.
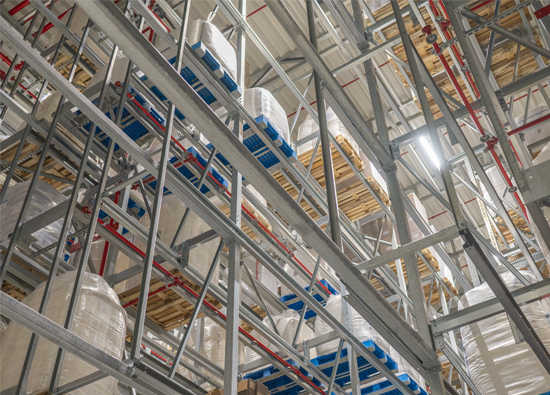
Hämmerle Kaffee GmbH decided to take an important step by investing 10 million euros in new buildings, intralogistics, and machines. The vending supply specialist wanted to focus particularly on international expansion. They needed a new solution as they had been confronted with unstable supply chains and insufficient space at their site in recent years. What's more, the company dispatches 150 – 350 pallets per day on average – at peak times, all staff had to help to ensure the orders were ready on time. To manage these quantities, both the flow of goods and handling needed to be optimized. Previously, the staff had to manually manage lists and perform the time-consuming process of gathering together the goods, as the company only had a very small, manual warehouse.
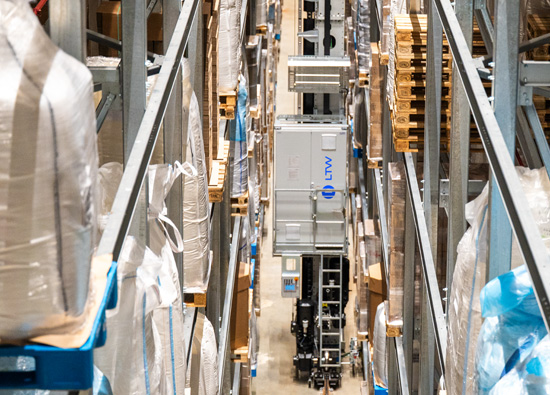
As a general contractor, Hämmerle Kaffee made it their mission to coordinate the entire expansion of the site independently. What does this mean? Every task in the project was allocated individually, making internal project management extremely time-intensive and resulting in many complex interfaces having to be managed. Not only this, but also the renovation took place while daily operations continued, which was very challenging for staff. To add to this there were also structural conditions that required a special solution for the conveyor system, as the picking areas are on different levels.
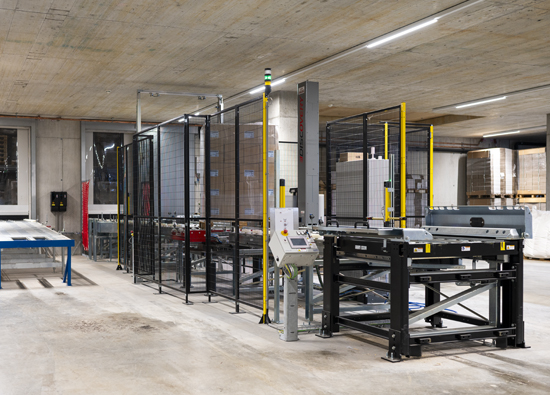
It was important to Hämmerle Kaffee to be able to guarantee their customers' delivery reliability. Thanks to the new HRL the goods are now centralized, production is possible at all times, the logistics workflows have been accelerated, and the company is now able to respond much more flexibly to their customers' needs. In addition, all the logistics processes run more seamlessly. A total of three stacker cranes (RBG) manage around 8,500 pallet storage locations. In the pre-zone of the picking stations, the goods are transferred to a transfer car. This has also been equipped with a lift to overcome the structural conditions. The goods then enter the HRL, where they are transferred to RBG1. This also functions as a vertical conveyor. The company settled on this cost-optimized solution as the performance requirement for the warehouse is lower, but the same distribution of the goods across the three rack aisles is necessary for structural reasons.