Halle, Germany
Back Shop
Founded in 1998 in Hamburg as a subsidiary of Harry-Brot, BACK SHOP can count on the support of Germany's second-largest manufacturer of baked goods for an extensive supply of goods – and on more than 325 years of ongoing tradition: Harry-Brot is in its tenth generation of private family ownership. BACK SHOP supplies food wholesalers, retailers, and bakeries with frozen bakery products. Seventy-five percent of the extensive product range comes from Harry-Brot, and is topped off by specialties from other manufacturers. The modern distributor understands that along with reliable product quality, its readiness to deliver is a key factor for success.
PROJECT OVERVIEW
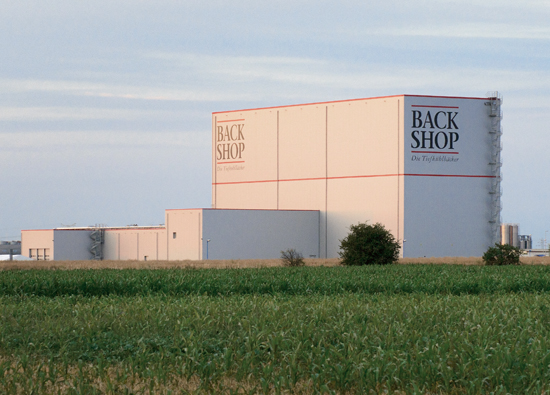
Anyone wanting to export bread overseas depends on impressive quality – and perfect frozen-food logistics. Planning for long-term future growth makes it obvious that the manual handling of the early days has reached its limits. This is because the demands of customized order picking are also increasing in the core market of Germany and eastern Europe – with ever smaller order quantities, shorter delivery times, and precise batch traceability. The high transport volume in relation to the value of the goods makes logistics errors a relevant cost factor.
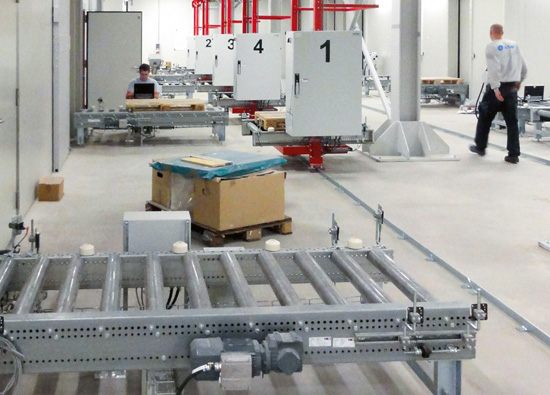
It does not take long to realize that the only way to implement the complex project is to use a full-service provider. To avoid overstretching the expertise of the bidders, the responsible planner advises tendering separately for the construction and intralogistics of the warehouse. The high-bay warehouse and the electric monorail system are planned for the spring, and the automated small-parts storage, conveyor system, and software for the fall, each time in two stages. LTW bids successfully for the intralogistics in both negotiations.
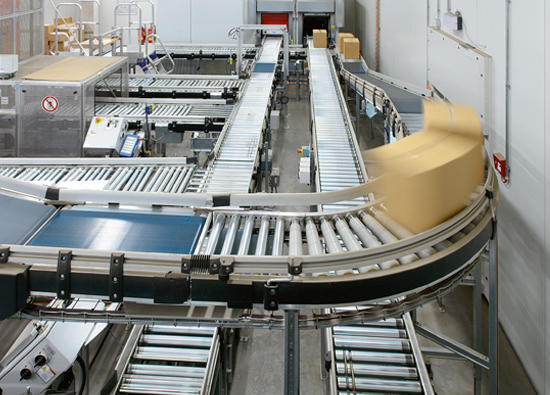
Each week, the project partners regularly fine-tune the details on the construction site, displaying the required flexibility. Despite delays in construction due to the weather, LTW brings the 35-meter-tall stacker cranes from their own manufacturing facility into the high-bay warehouse through the roof in May. The mechanical components of the conveyor system are bought in from approved partners. The LTW team programs the control system, and once installed, brings all parts of the system together to form a homogeneous material flow.