Wolfurt, Austria
Haberkorn
As a family enterprise founded in 1932, Haberkorn is now among the largest technical dealers in Europe in the fields of industry, construction, and special products. With its headquarters in Wolfurt (AT), the technical dealer supplies industrial and construction companies with PPE, lubricants, and technical products such as hoses, machine elements, and hydraulics. Haberkorn employs more than 2,200 staff at over 30 sites in Austria, Germany, Eastern Europe, and Switzerland. In 2020, the group of companies achieved a turnover of 626 million euros.
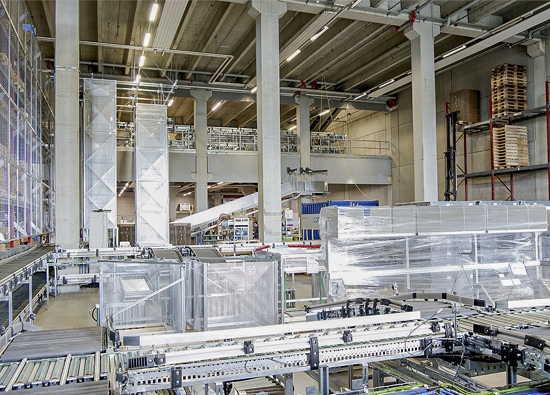
As an ever-growing company with successful business developments in recent years, the company with headquarters in Wolfurt has reached its capacity limits. As customer requirements have become increasingly specific and the handling of goods has thus become more complex, Haberkorn needed to take action. In order to meet its needs in-house and the requirements of its customers, a fully automated logistics center is the solution. The new warehouse should not only make work considerably easier, but also speed things up a lot. The goal was to manage the planned growth with the fully automated logistics expansion and be well-equipped for the future.
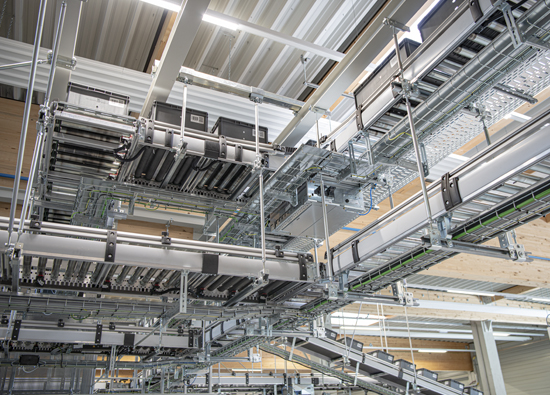
The main goal of this project was to increase efficiency in intralogistics. The logistics center that has grown steadily over the years has not only become more comprehensive, but also more complex. The greatest challenge was therefore in mapping all necessary processes in the new technology and planning the perfect material flow. Extensive coordination between the existing software from an external supplier and the LTW components was also needed. Close collaboration was required here to implement complex process changes and upgrade the existing software accordingly.
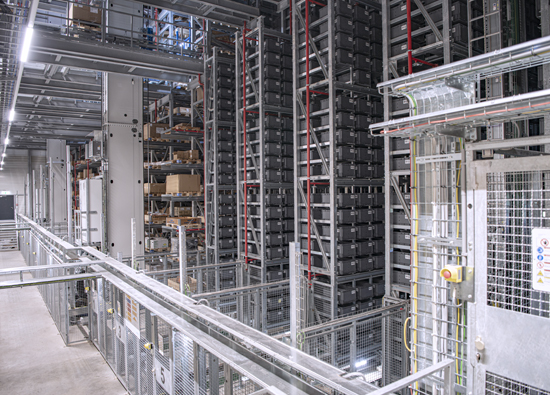
The end result is a spacious warehouse complex with two separate high bay warehouses and the connected conveyor system. The pallet warehouse with around 11,300 storage locations is operated by six aisle-bound stacker cranes. The container warehouse also provides space for 64,000 boxes with ten stacker cranes. The extensive conveyor system with 18 goods-in stations, 16 picking stations, 20 packing stations, and 9 vertical conveyors meets the requirements. The customer is more than satisfied with the end result. Right from the start, the most important requirement for the customer was increasing the efficiency of their logistics processes. With our intralogistics solution, we were able to fulfil the customer's request.