Bremen, Germany
ZF Services
ZF Services is a leading global technology group for driveline and chassis technology, with 121 production companies in 26 countries. With around 75,000 employees, the group achieved a turnover of almost 17.4 billion euros in 2012. The entire product portfolio is geared to ensuring the performance and efficiency of vehicles throughout their life cycle. The driveline and chassis technology is commercially available under the established product brands of Sachs, Lemförder, Boge, and ZF Parts.
PROJECT OVERVIEW
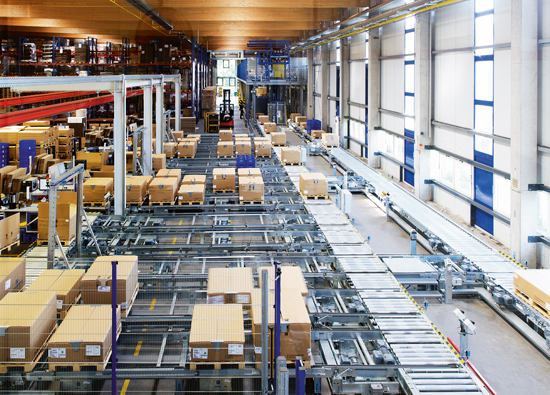
When ZF Services starts the planning process for an automatic high-bay warehouse, future maintenance is already an important consideration, because as after-sales specialists themselves, they know all about the issue of customer service. A sustained increase in sales volume, as well as customer demands, also raise awareness of the risks of supply disruption at ZF. Not only that, but after 12 years of operating an automated small-parts warehouse, they have plenty of positive experience relating to preventive maintenance, performance, and running costs.
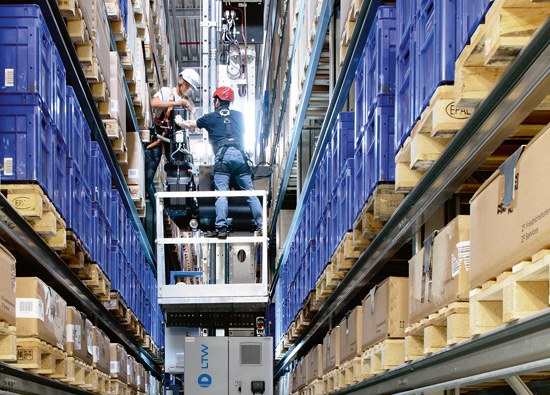
During contract negotiations, it becomes obvious that the customer needs an all-inclusive maintenance agreement: a 24-hour hotline on six days a week, with a one-hour response time – and guaranteed availability of 99%. Well thought-out spare parts management is necessary to meet this difficult target. Synergies from an affiliated project, where LTW supplied six stacker cranes to the ZF headquarters in Schweinfurt, are of interest here.
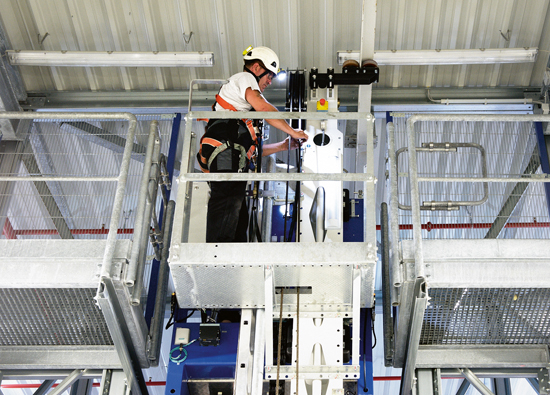
Admittedly there is a distinct difference in the overall heights of the two logistics centers – 44 m in Schweinfurt and 12 m in Bremen – but LTW can nevertheless design many components that are suitable for both systems. This will allow critical spare parts, as well as the necessary know-how, to be quickly transferred between the two locations later on. Immediately before commissioning, an LTW training specialist teaches the six-strong ZF Services maintenance team about the system. The planned maintenance work follows a clear pattern: two weekends, twice a year.