Feldkirch, Austria
Bischof Lebensmittellogistik
The development of the Vorarlberg-based logistics service provider is closely linked to the regional expansion of the food industry. Bischof provides a comprehensive range of services for customers such as Kraft Foods, 11er, Hilcona, Bofrost, and Ölz: from collecting frozen and refrigerated foods, to payment of duty, storage, order picking, and assembling, to co-packing, retrieval, and on-time delivery to wholesale chains and retailers throughout Europe. The backbone of the cold chain is currently formed by 260 employees, 190 refrigerated trucks, and 25,000 pallet spaces; 16,000 of which are for frozen food.
PROJECT OVERVIEW
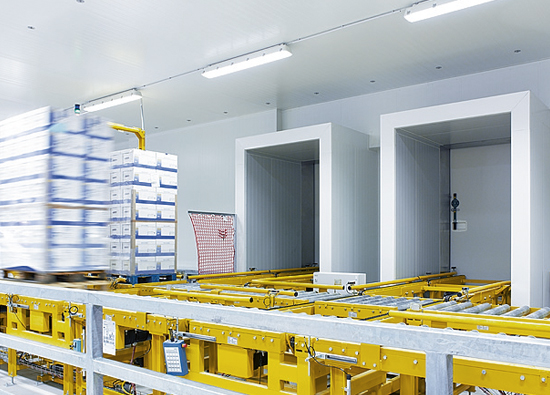
Bischof decides to double its storage capacity and build a fully automated deep-freeze high-bay warehouse. Key customers, including 11er and Kraft Foods, are indicating a rapid increase in demand, at the same time as suggesting who should implement the project: LTW Intralogistics! Thanks to their outstanding references in the frozen food sector, LTW is awarded the contract to supply stacker cranes, conveyor systems, and warehouse management software.
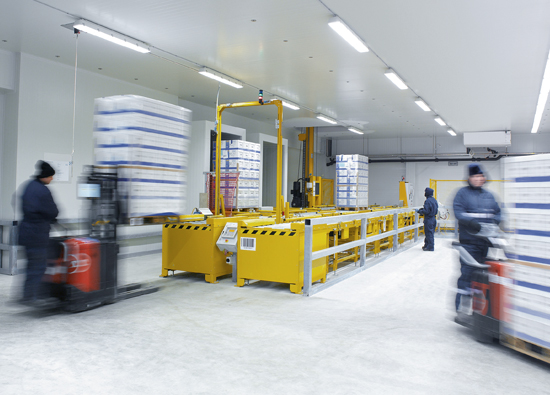
Fully automated operation of a logistics system at -28°C in the high-bay warehouse and -5°C in the pre-zone demands a high standard of planning and equipment design. Experience is essential for correctly estimating material shrinkage, and for paying attention to important details – from choosing a suitable gear oil for cold temperatures, to deciding which heatable electrical components to use.
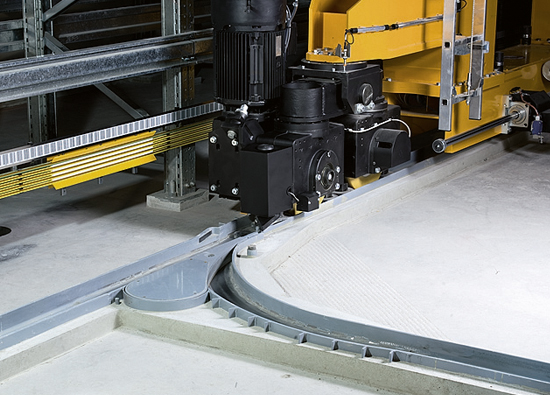
The flow of goods in the 4-aisle, double-depth high-bay warehouse is implemented by two aisle-switching stacker cranes – the LTW warehouse control system ensures that there are no collisions. Every rack aisle is connected to the conveyor systems at the front. Two transfer cars bridge the storage and retrieval lines. A vertical conveyor connects the order picking area on the upper floor to the material flow below. Features such as contour check and buffer locations ensure smooth operation.